- Home
- Techniques
- PECM
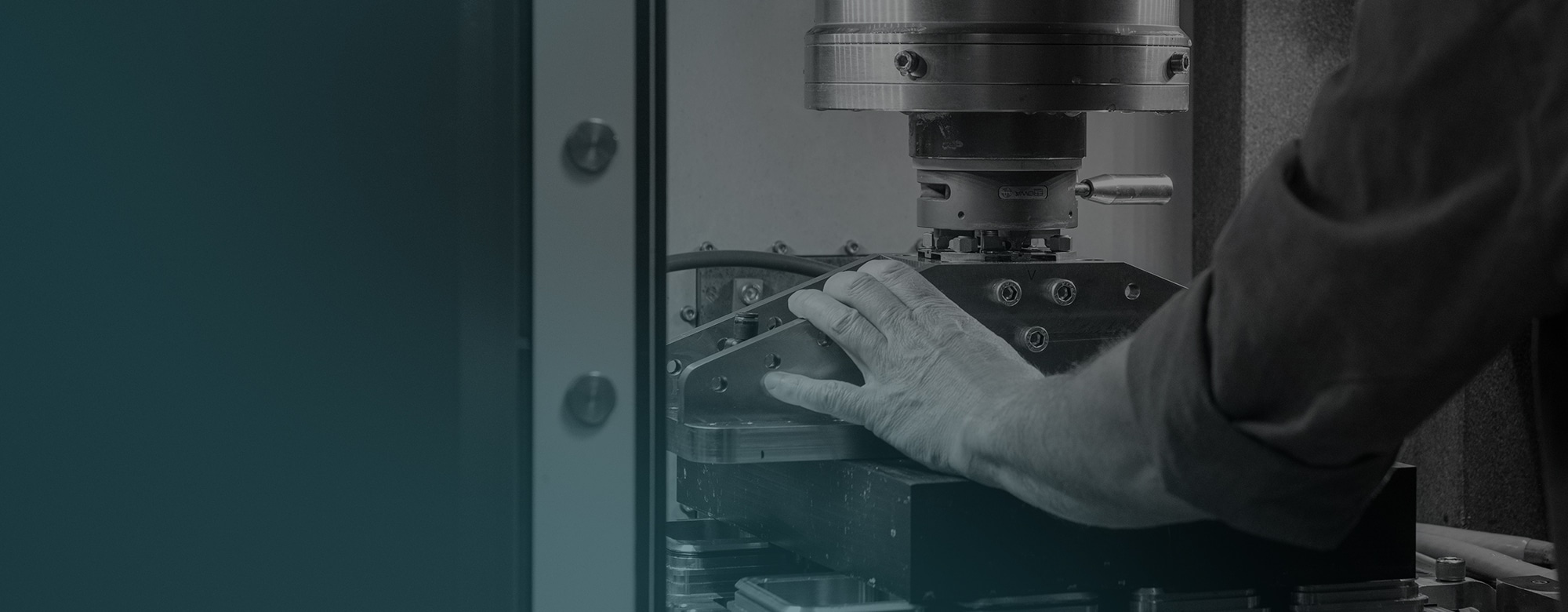
PECM: new possibilities for extreme precision
PECM is a new and innovative machining technique that allows products to be machined efficiently and with extreme accuracy. Whereas other machining techniques cut away parts of a material, the groundbreaking PECM technique dissolves the material. Since 2016, Ter Hoek has been the exclusive PEM Application Center for the Benelux on behalf of PEMTec.
Using this advanced technology means always delivering custom solutions.
Our expertise, combined with our modern machinery, makes Ter Hoek your specialist in PECM solutions. Please read below what PECM entails and what we can do for you with PECM.
PECM is a new and innovative machining technique that allows products to be machined efficiently and with extreme accuracy. Whereas other machining techniques cut away parts of a material, the groundbreaking PECM technique dissolves the material. Since 2016, Ter Hoek has been the exclusive PEM Application Center for the Benelux on behalf of PEMTec.
Using this advanced technology means always delivering custom solutions.
Our expertise, combined with our modern machinery, makes Ter Hoek your specialist in PECM solutions. Please read below what PECM entails and what we can do for you with PECM.
What is PECM?
PECM (Precision Electro-Chemical Machining) is a highly advanced machining technology with a high degree of reproducibility, allowing products to be machined to high precision (with an accuracy of up to 0.002 mm). Electrical tension causes the material to dissolve in a controlled manner and form an electrolyte, which conducts the electrical current. This makes the technique suitable for many electrically conductive materials.
Unlike machining techniques such as wire EDM, no heat is released during the PECM process. As a result, no mechanical or thermal stress is exerted on the material. In addition, no contamination of the material occurs because the workpiece and the electrode do not come into contact. PECM is thus very suitable for mechanically highly-stressed workpieces whose end result must not contain microcracks or contamination from foreign materials in the surface.
Engineers be aware: most parts are designed for known production techniques, PECM allows you more freedom in design!
PECM VS Other techniques
- No heat-induced zone
- No microcracks
- No stress
- No contamination
- High surface quality
- Low tool wear
- High reproducibility
The video demonstrates how PECM works. The electrode used during PECM is a negative form of the desired product and moves toward the workpiece in a pulsating motion. The electrolyte, a chemical compound that includes a saline solution in water, is pressure-pumped through the opening between the workpiece and the electrode. The parts of the workpiece that have dissolved are thus safely washed away and no longer come into contact with the workpiece.
The tremendous accuracy of PECM allows for an extremely low roughness value (0.03 Ra). Surfaces with such a low roughness value have a smooth surface, making them easy to clean, among other things. This is essential for products used for medical technology, for example. The closed structure of the surface means that medicine residues are not left behind, preventing cross-contamination of different medicines.
PECM (DIS)advantages
PECM has numerous advantages. However, there are also some disadvantages, like longer engineering and prototyping phase. But: high reproducibility and multi-processing tools lower the product price, making PECM a reliable and cost efficient production method!
PECM ADVANTAGES
- Electrode wear very low
- Suitable for large series
- Cold process, process temp 20 - 50°C
- Clean process, contact-free from the electrode
- Lower product price
- Process is highly reproducible
- Absolutely burr-free
- Without micro-cracks and structural changes
- Without thermal or mechanical influences
- Complex geometries can be produced precisely and formally
- Surface roughnesses of Ra>= 0.02 µm
PECM DISADVANTAGES
- Multi-processing tools (multiple electrodes) are demanding
- Longer engineering and prototyping phase
- Determine correct technology and flushing conditions
- Machining only possible in Z-axis
- Part size limitation
- Precious metals are not workable
- Always finishing radius on edges
Why PECM by Ter Hoek?
At ter Hoek all PECM Tooling is designed and manufactured in-house using all the machining techniques that are available to reach the precision needed for high-end PECM tooling. Often tools evolve from a simple testing tools to a single-piece tool and then to large series production tools.
Since 2016, Ter Hoek has been the exclusive PEM Application Center for the Benelux on behalf of PEMTec. PEMTec is a global organization that develops machines for this form of electrochemical precision machining. During the years we have gained a lot of experience you can benefit from. And, as an AS9100-certified specialist, we can realize any customer’s wish in the field of tooling and series manufacturing.
masterclass PECM
Twan Altena is application engineer PECM at Ter Hoek. In this online masterclass he will explain about PECM versus other techniques, the PECM process, technical specifications, what types of metal can be processed with PECM, the surface quality, and cleanliness. He also shares valuable ins and outs around cases. How did he face problems and think of the solution needed? Why is tooling so important? Click on the link to find out more about this on-demand masterclass: https://info.terhoek.com/en/pecm-masterclass-on-demand.
What are the costs for PECM?
The costs of PECM depend on a variety of factors, such as the desired precision, shape, and material used. There may be additional costs associated with the PECM technique because a test tool must first be made. Nevertheless, PECM can be more economical than other machining techniques, especially for the series manufacturing of large numbers of parts that must meet high-quality requirements. With our extensive knowledge of precision components, we are guaranteed to offer you the best custom solution.